Manufacturing Facilities
. Our operations serve as our headquarters and are geared for low volume components to medium volume operations. It is integrated for engineering and tool design, mold making, debinding, sintering and certain finishing and assembly operations.
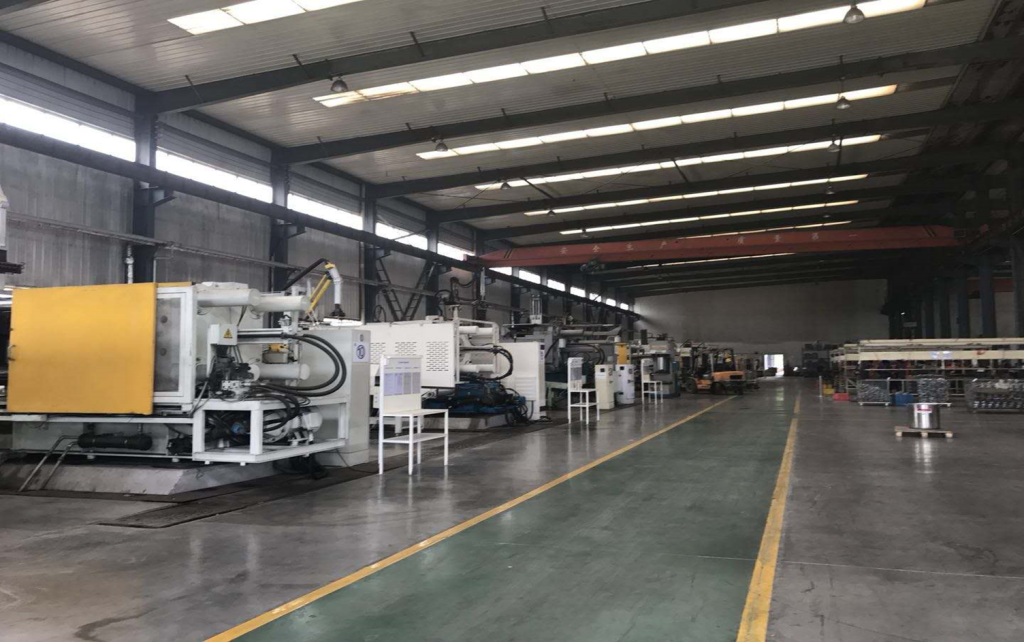
What we Do?
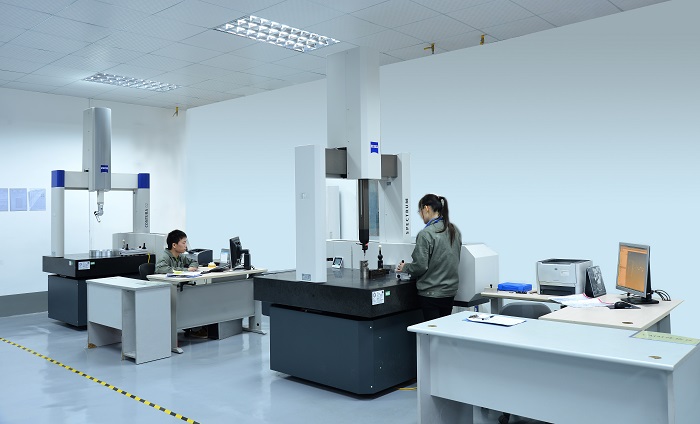
Metal Injection Molding materials
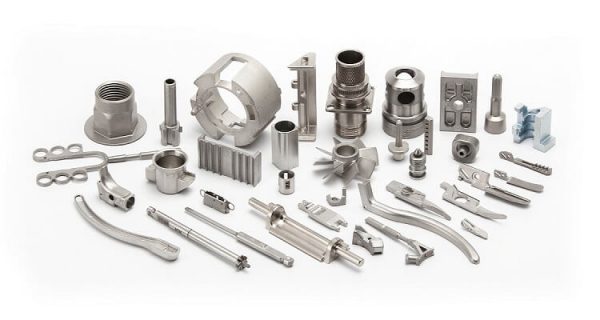
a full range of materials that are useful for a wide variety of applications. Many of these materials can be heat treated to meet specific mechanical properties for the individual application. Post treatment options such as Hot Isostatic Pressing (HIP) can further enhance mechanical properties for the most demanding applications.Low carbon and high alloy steels for case and through hardening requirements, a full range of austenitic, ferritic, martensitic and precipitation hardening stainless steels, soft magnetic alloys as well, Co and Ni base super alloys and select non-ferrous alloys.
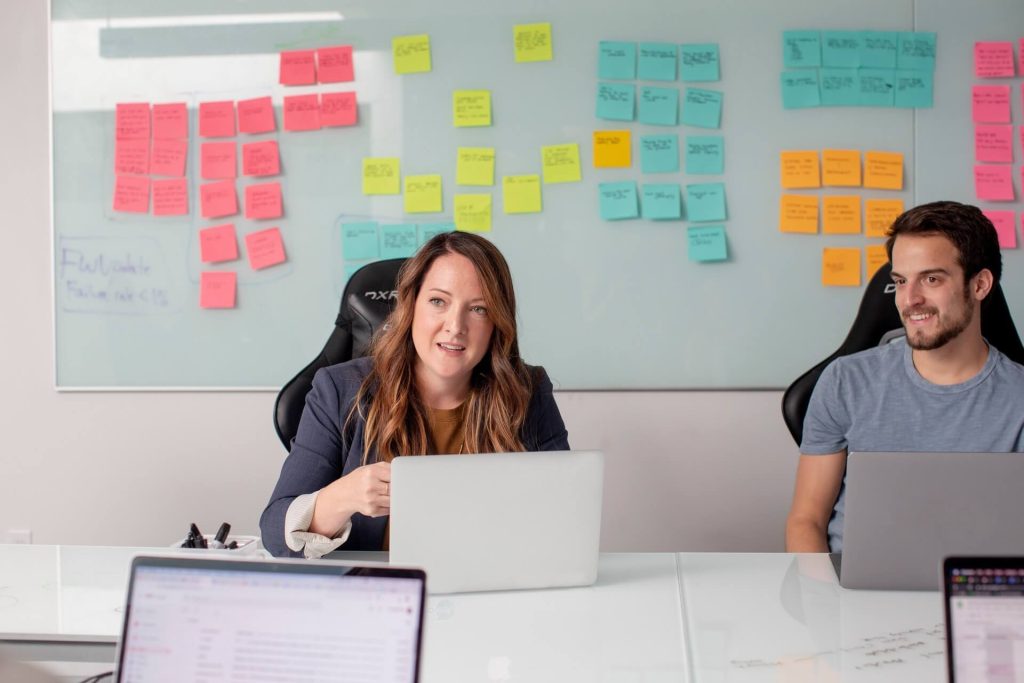
Team Members
Growing result
Happy Client
Business Done
Quality without compromise
Greata’s approach towards quality follows several basic principles: strategic planning and leadership, a strong focus on the customer, fact-based management, continuous improvement and total employee involvement.
Our quality system, combined with a refined business system provides the fundamental structure for meeting and exceeding our customers’ needs and expectations. Because our ongoing improvement efforts focus on refining our processes and controls, we are able to provide the highest quality and service in the industry.
Quality without compromise
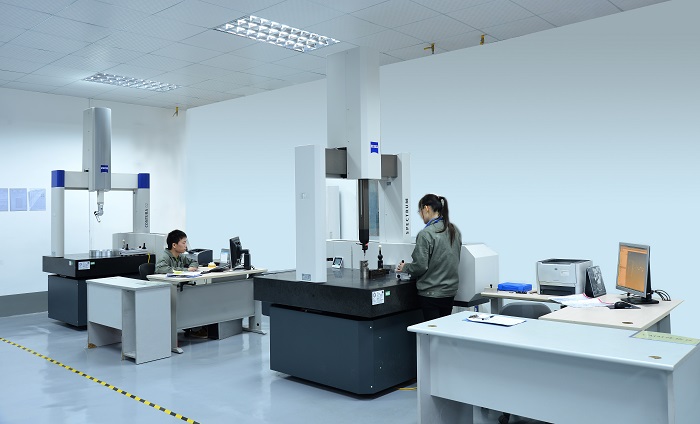
Precision Machining
Greata provides a full range of value added Metal Injection Molding (MIM) services to supply fully finished / machined parts and assemblies.
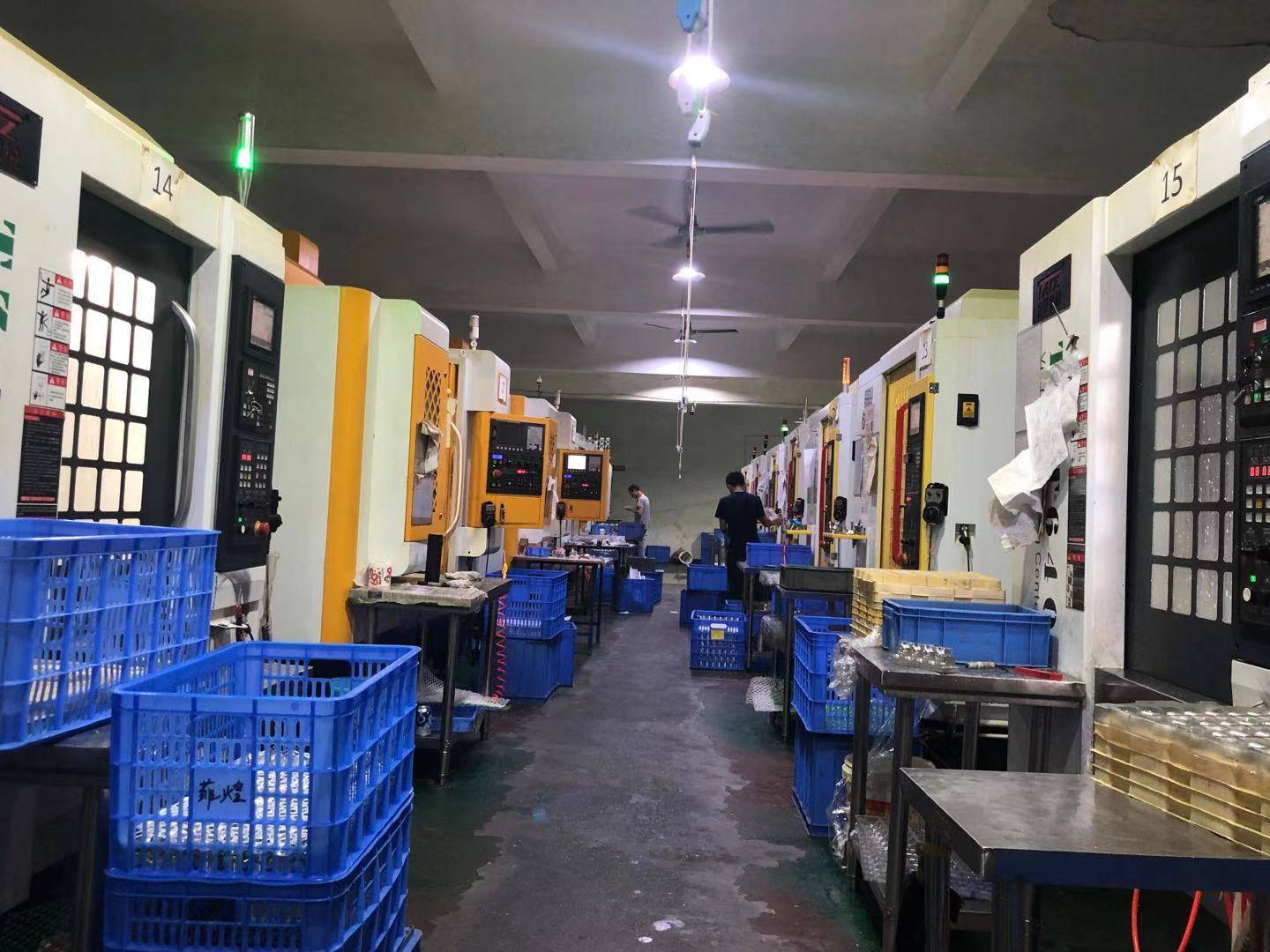
We administer a complete range of heat-treating services for our products. Our equipment is modern and precisely controlled which allows us to process a wide variety of case hardening and through hardening alloy steels as well as a complete range of martensitic and precipitation hardening stainless steels.
- Vacuum heat-treating and annealing.
- Sealed quench heat-treating and atmosphere tempering.
- Case hardening.
- Ion and gas nitriding.
- Various organic coatings.
- Hot Isostatic Pressing (HIP) to attain full density for demanding applications.
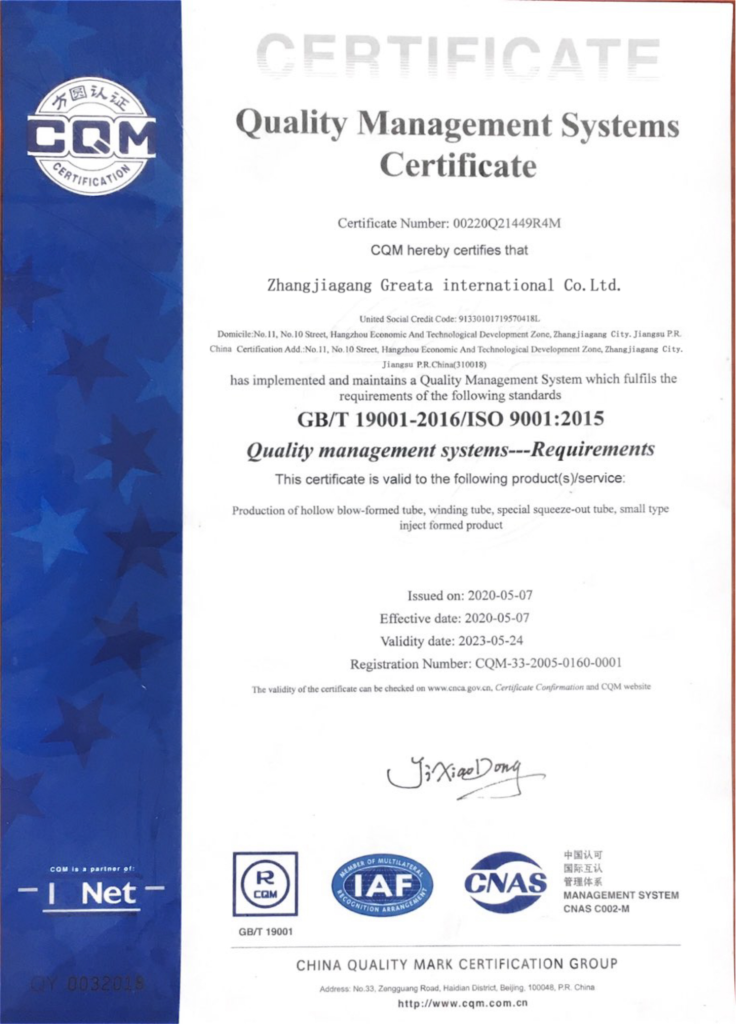