Production of prototypes for sheet metal
Sheet metal manufacturing can be used to create either functional prototypes or consumer parts, but consumer parts typically require a finishing process before they are ready for market.
Advantages of sheet metal production
Material selection Aluminium + ,
Copper, Stainless Steel +-Steel and Zinc2 Finishing Options Beading, Anodizing, Coating, Powder Coating and Custom Surfaces
Thickness options
Various instruments4 Durability
Sheet metal manufacturing produces durable parts for prototyping or end use
Scalability Low setup costs mean low prices for large volumes6 turnaround parts delivered in just 5-10 days
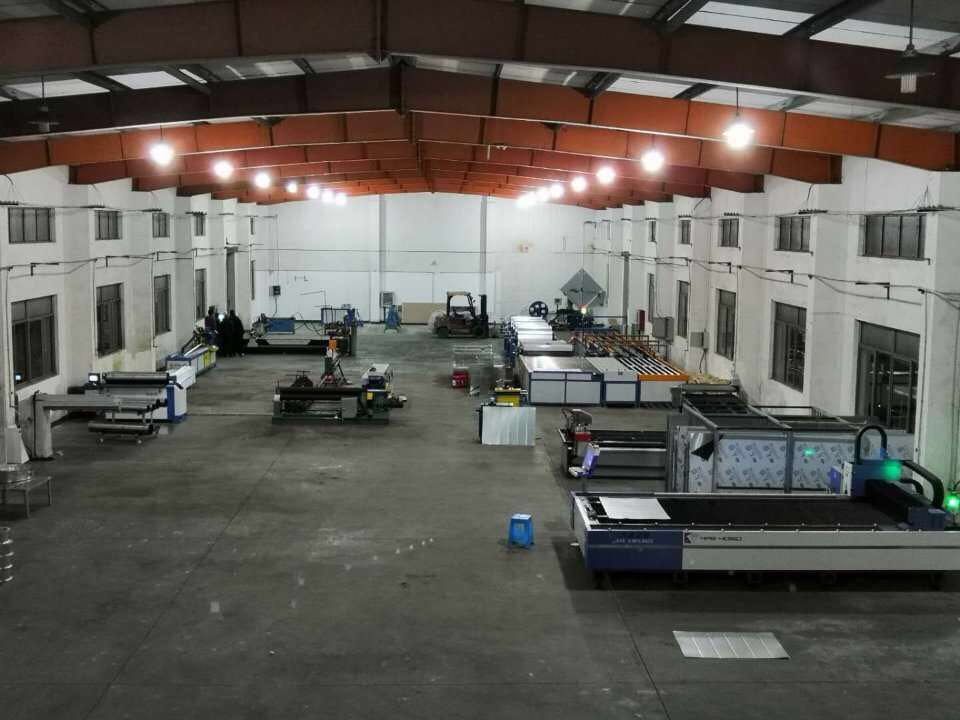
There are several processes that fall under the umbrella of ‘sheet metal fabrication’. These include cutting, bending and punching, and can be used either in tandem or individually.
Sheet metal fabrication can be used to create either functional prototypes or end-use parts, but end-use sheet metal parts generally require a finishing process before they are ready for market.
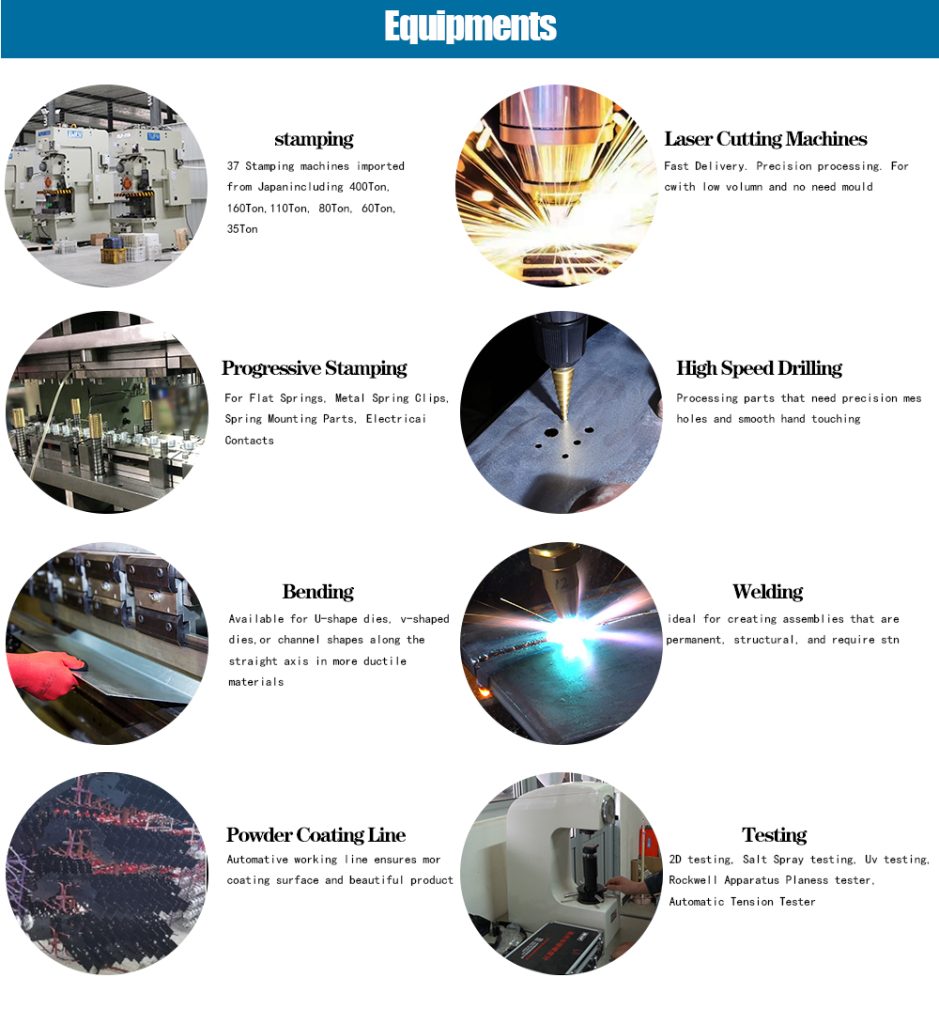
Does it cost more to use several sheet metal forming processes?
In general, a part that is cut, bent and punched costs more than a part that is simply cut with a laser cutter, for example.
However, most sheet metal parts require a combination of forming processes, which does not dramatically increase the price.
Is there a minimum order quantity?
No, you can order a one-time prototype or 1,000+ units.
What is Sheet Metal Fabrication?
Create List
Create User
Engage Visitor
Sheet Metal FAQ
Do I need laser cutting, waterjet cutting or plasma cutting?
The type of cutting machine used depends on the chosen material and thickness of the sheet, as well as factors such as desired lead time and tolerances.
We know which projects need which equipment, so you don’t have to specify a specific cutting machine.
What is sheet metal processing?
Sheet metal manufacturing is a series of manufacturing processes used to transform sheet metal material into functional parts. The sheet metal is usually between 0.006 and 0.25 inches (0.015 and 0.635 centimeters) thick.
There are several processes that fall under the umbrella of “sheet metal production”. These include cutting, bending and punching and can be used either in tandem or individually.
Sheet metal manufacturing can be used to create either functional prototypes or consumer parts, but consumer parts typically require a finishing process before they are ready for market.
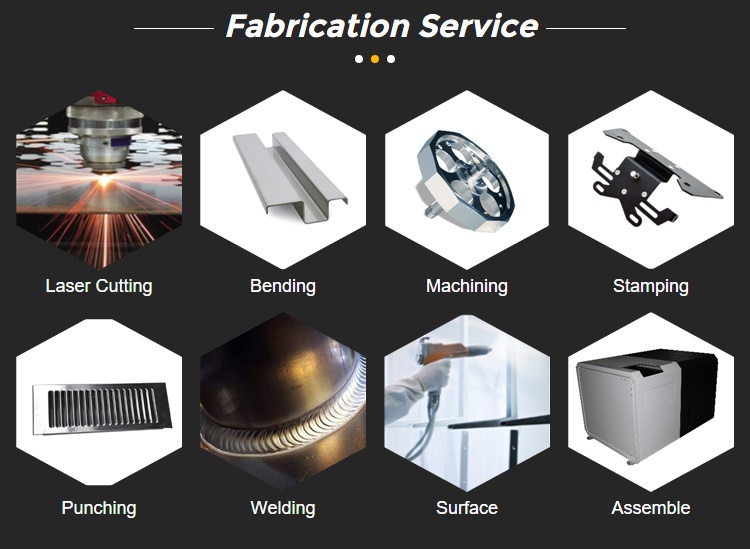