Vacuum Casting – Urethane Casting
Additive Manufacturing
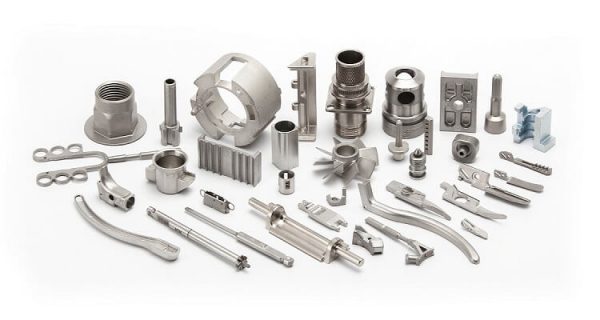
Binder Jet 3D Printing
3D Production Design
the Binder-Jet 3D printing process is an evolution of another decade + older AM process called Direct Metal Laser Sintering (DMLS). Binder-Jet 3D printing enables the production of proto-samples within days, involves no upfront tooling costs. The process allows infinite design changes during product development without time delay helping the design engineers to get to their optimum design quickly and at the lowest cost.
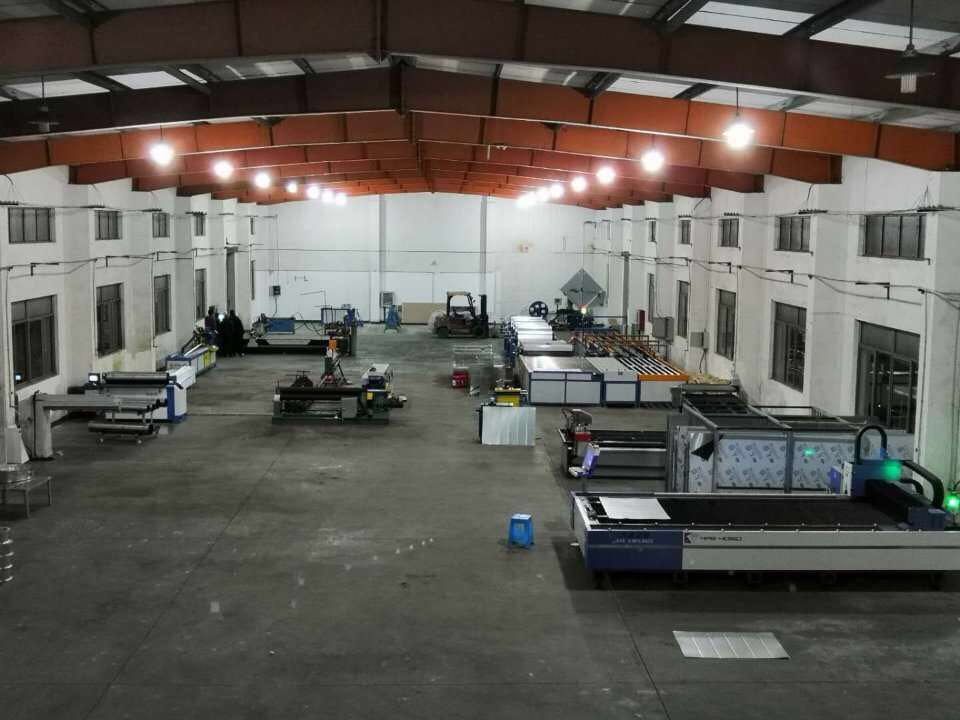
Laser Powder Bed Fusion
Production Design
Laser powder bed fusion (LPBF) is a type of additive manufacturing (also known as 3D printing) process that uses a laser to melt and fuse together metallic powders to create three-dimensional objects. The process involves laying down successive layers of powder and using a laser to melt and fuse the material in specific areas to build up the desired shape.
In LPBF, a bed of metallic powder is first spread out on a build platform. The laser then traces the cross-sectional pattern of the desired object onto the bed of powder, melting and fusing the material together to create the first layer. The build platform then lowers slightly and a new layer of powder is spread on top of the previous layer. The process is repeated until the entire object has been built up.
LPBF is commonly used to create metal parts and has a number of advantages over traditional manufacturing methods, including the ability to create complex geometries and the ability to produce parts with high accuracy and repeatability. It is also capable of producing parts with high surface finish and good mechanical properties. However, the process can be slow and may require extensive post-processing to remove excess powder and smooth the surface finish.
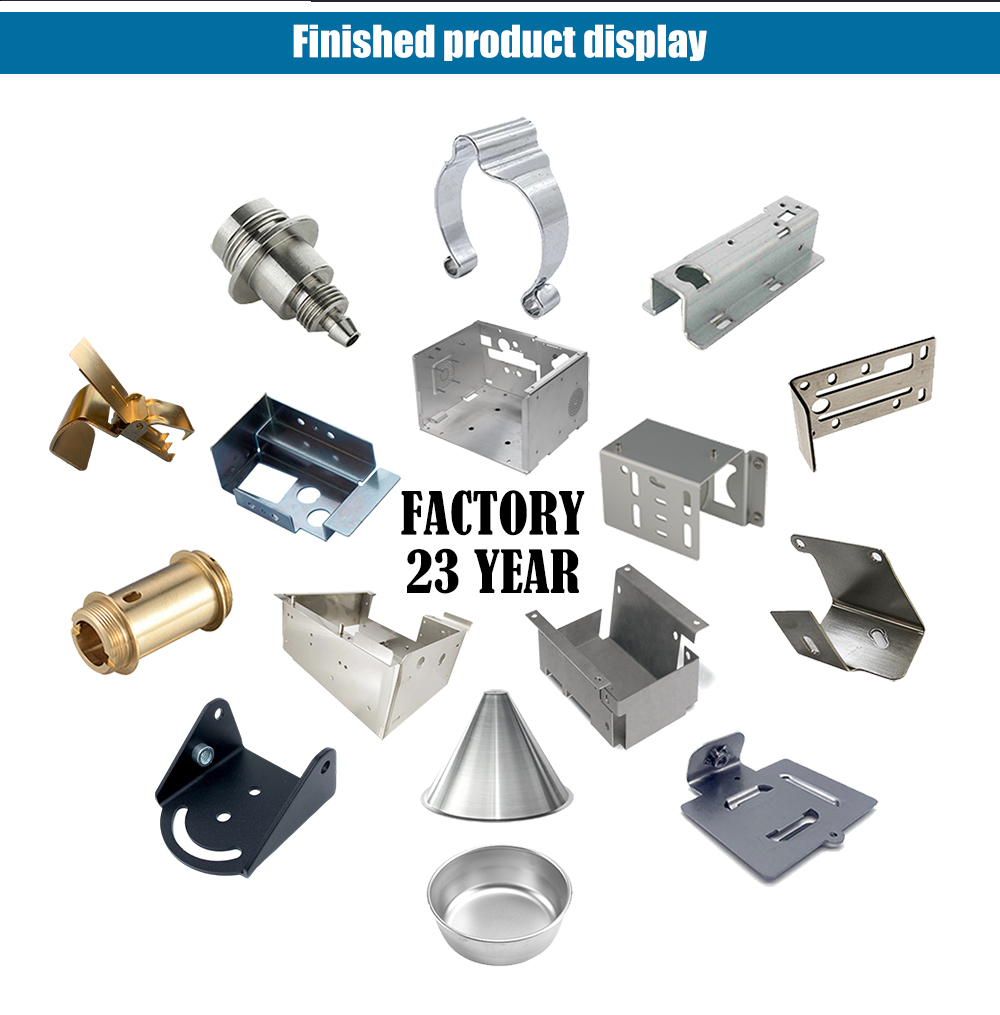
Sheet Metal Fabrication
Production Design
Sheet metal fabrication is a process that involves cutting, bending, and assembling sheet metal to create a wide range of products and structures. The process begins by selecting the appropriate type and thickness of sheet metal for the product or structure being fabricated. Then, the sheet metal is cut to size using a variety of methods, including laser cutting, waterjet cutting, and punch press cutting. Next, the sheet metal is bent and shaped using a press brake or other machine to form the desired shape. Finally, the sheet metal is assembled using a variety of methods, including welding, riveting, and fastening with screws or bolts.
There are many industries that rely on sheet metal fabrication, including automotive, aerospace, construction, and appliance manufacturing. Sheet metal fabrication is used to create a wide range of products, including car bodies, airplane wings, building facades, and appliances such as refrigerators and washing machines.
The tools and equipment used in sheet metal fabrication can vary depending on the size and complexity of the product being fabricated. Smaller fabrication shops may use manual tools such as shears and punches, while larger shops may use more advanced equipment such as computer numerically controlled (CNC) machines.
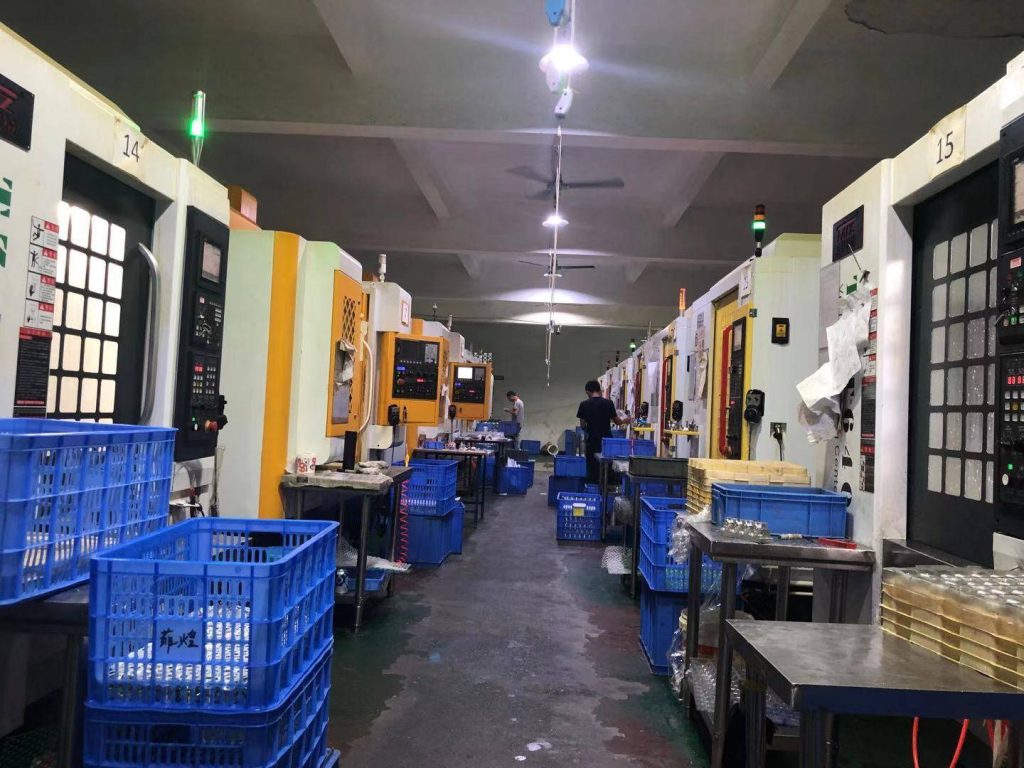
Metal Injection Molding materials
Production Design
Metal injection molding (MIM) is a manufacturing process that involves injecting a feedstock made of metal powders and binder material into a mold cavity. The feedstock is then heated and injected into the cavity, where it hardens to take the shape of the mold. The most commonly used materials for metal injection molding are stainless steel, low-alloy steel, and soft magnetic alloys. These materials offer a good combination of strength, ductility, and corrosion resistance, making them suitable for a wide range of applications. Other materials that can be used in metal injection molding include titanium, cobalt-chromium alloys, and tungsten alloys.